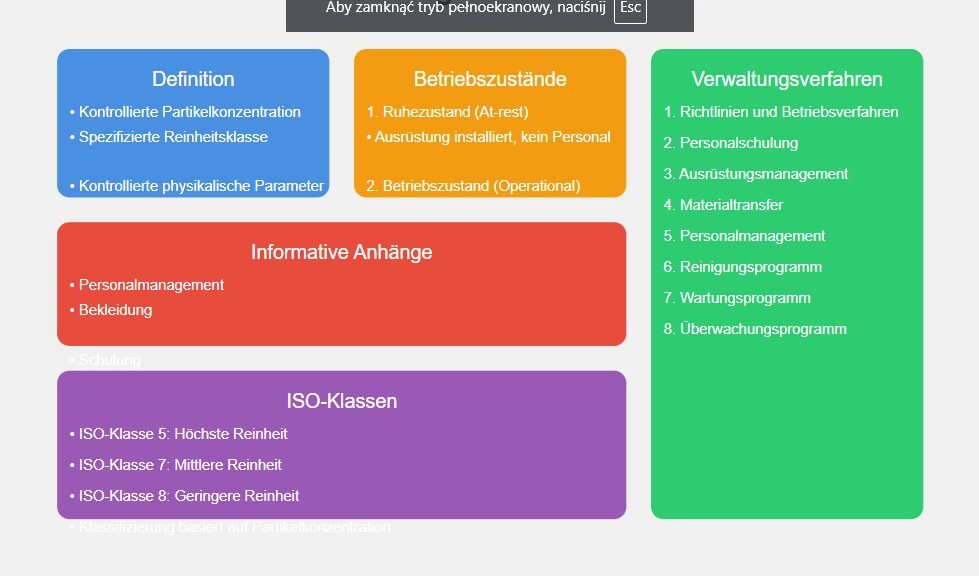
Reinräume ISO 8, ISO 7, ISO 5 – aus der Sicht eines Praktikers
By krzluk | | Comments 12 comments
Dieser Artikel basiert auf den Erfahrungen des Autors, der 15 Jahre lang Reinräume der ISO-Klasse 5, ISO-Klasse 7 und ISO-Klasse 8 gemäß ISO DIN 14644-1 verwaltet hat. Die hier zusammengetragenen Informationen spiegeln die praktischen Erkenntnisse und bewährten Verfahren wider, die sich aus der langjährigen Arbeit mit verschiedenen Reinraumklassen ergeben haben. Diese Erfahrungen unterstreichen die Bedeutung einer sorgfältigen Planung, konsequenten Umsetzung und kontinuierlichen Überwachung aller Aspekte des Reinraummanagements, um die hohen Standards der ISO DIN 14644-1 zu erfüllen und aufrechtzuerhalten.
Reinräume: Definition, Zustände und Verwaltung gemäß ISO 14644-1
Definition eines Reinraums
Ein Reinraum ist laut ISO DIN 14644-1 ein Raum, in dem die Konzentration luftgetragener Partikel kontrolliert und klassifiziert wird. Reinräume werden so konzipiert, gebaut und betrieben, dass die Einführung, Erzeugung und Retention von Partikeln im Raum kontrolliert werden. Die Klasse der luftgetragenen Partikelkonzentration wird dabei spezifiziert.
Neben der Partikelkonzentration können in Reinräumen auch andere Reinheitsattribute wie chemische, lebensfähige oder nanoskalige Konzentrationen in der Luft sowie die Oberflächenreinheit hinsichtlich Partikel-, Nanoskala-, chemischer und lebensfähiger Konzentrationen spezifiziert und kontrolliert werden. Zusätzlich können je nach Anforderung auch andere relevante physikalische Parameter wie Temperatur, Feuchtigkeit, Druck, Vibration und elektrostatische Aufladung kontrolliert werden.
Betriebszustände von Reinräumen
Die ISO DIN 14644-1 definiert zwei wichtige Betriebszustände für Reinräume:
- Ruhezustand (At-rest): In diesem Zustand ist der Reinraum oder die Reinraumzone vollständig mit installierter und in vereinbarter Weise betriebener Ausrüstung ausgestattet, jedoch ohne anwesendes Personal.
- Betriebszustand (Operational): Dies ist der vereinbarte Zustand, in dem der Reinraum oder die Reinraumzone in der spezifizierten Weise funktioniert, mit laufender Ausrüstung und der festgelegten Anzahl von Personen.
Verwaltung von Reinräumen: Wichtige Verfahren
Bei der Verwaltung von Reinräumen gemäß ISO DIN 14644-1 sollten folgende Aspekte in den Verfahren berücksichtigt und beschrieben werden:
- Einrichtung eines Systems zur Definition von Richtlinien und Betriebsverfahren zur Aufrechterhaltung der Reinheitsgrade
- Schulung des Personals
- Transfer, Installation und Wartung stationärer Ausrüstung
- Ein- und Ausbringen von Material und tragbarer Ausrüstung in den Reinraum
- Aufrechterhaltung eines Personalmanagemmentprogramms, einschließlich eines Bekleidungsprogramms
- Durchführung eines Reinigungsprogramms, das spezielle Reinigungsanforderungen berücksichtigt
- Implementierung eines Wartungsprogramms für den Reinraum
- Etablierung eines geeigneten Überwachungsprogramms
Zusätzlich werden in der ISO DIN 14644-1 informative Anhänge zu folgenden Themen bereitgestellt:
- Personalmanagement
- Bekleidung
- Schulung
- Reinigung
Auswirkungsbeurteilung für Reinräume: Erkenntnisse aus 15 Jahren Praxis
Einführung in die Auswirkungsbeurteilung
In meinen 15 Jahren als Reinraumexperte bei Reinräume GmbH habe ich die zentrale Bedeutung der Auswirkungsbeurteilung für den Erfolg unserer Reinräume erkannt. Zu Beginn meiner Karriere unterschätzten wir ihre Wichtigkeit, was zu unerwarteten Komplikationen führte. Heute bildet sie das Fundament unseres Qualitätsmanagementsystems für die ISO 5, 7 und 8 Reinräume. Wir führen sie nicht nur vor der Inbetriebnahme durch, sondern auch bei wesentlichen Veränderungen. Diese vorausschauende Strategie hat sich als unschätzbar wertvoll erwiesen, um potenzielle Risiken frühzeitig zu identifizieren und zu minimieren. Die größte Herausforderung war es, alle Beteiligten von der Notwendigkeit dieses umfassenden Prozesses zu überzeugen.
Entwicklung unserer Beurteilungsmethodik
Unsere anfängliche Methodik war zu starr und vernachlässigte wichtige Faktoren. Wir erkannten schnell, dass ein flexibler, ganzheitlicher Ansatz unerlässlich ist. Heute basiert unsere Auswirkungsbeurteilung auf einer umfassenden Datenbasis, die Konstruktionsdaten und Umgebungsparameter einbezieht. Eine besondere Schwierigkeit war es, die komplexen Wechselwirkungen zwischen Reinraumumgebung, Produkten und Prozessen zu verstehen. Durch intensives Training und den Austausch mit anderen Experten konnten wir unsere Analysefähigkeiten erheblich verbessern. Ein Wendepunkt war die Einführung von Simulationssoftware, die uns half, verschiedene Szenarien durchzuspielen und ihre Auswirkungen besser zu verstehen.
Schlüsselelemente der Beurteilung und ihre Herausforderungen
Die Analyse des Betriebsprogramms erwies sich als besonders komplex. Anfänglich übersahen wir oft kritische Details in unseren Verfahren. Ein Durchbruch war die Bildung von abteilungsübergreifenden Teams, die verschiedene Perspektiven einbrachten. Die Integration der ISO 14644-18 für Verbrauchsmaterialien stellte uns vor Herausforderungen, da spezifische Schulungen fehlten. Als Lösung entwickelten wir interne Schulungsprogramme, die sich als sehr effektiv erwiesen. Der Materialtransfer war ein weiterer Stolperstein. Unsere ersten Protokolle waren zu umständlich und wurden oft umgangen. Durch iterative Verbesserungen und Feedback vom Personal gelang es uns, praktikablere Lösungen zu entwickeln. Eine wichtige Erkenntnis war, dass selbst kleine Änderungen im Materialfluss große Auswirkungen auf die Reinraumleistung haben können.
Personalmanagement: Lehren aus der Praxis
Das Personalmanagement erwies sich als kritischer Faktor, den wir anfangs unterschätzten. Strenge Richtlinien für den Personaleintritt und -austritt waren zwar einfach zu implementieren, aber schwierig durchzusetzen. Wir lernten, dass regelmäßige Schulungen und klare Kommunikation entscheidend sind. Unser Bekleidungsprogramm durchlief mehrere Iterationen, bis wir die richtige Balance zwischen Schutz und Komfort fanden. Eine wichtige Erkenntnis war, dass das Wohlbefinden des Personals direkten Einfluss auf die Reinraumleistung hat. Die Einführung von Erholungszonen und flexiblen Schichtplänen führte zu einer signifikanten Verbesserung der Compliance und Produktivität. Eine unerwartete Herausforderung war der Umgang mit psychologischen Faktoren wie Claustrophobie in Reinräumen, was uns dazu veranlasste, spezielle Unterstützungsprogramme zu entwickeln.
Betriebszustände und Notfallszenarien: Vorbereitung zahlt sich aus
Die Berücksichtigung verschiedener Betriebszustände in unserer Beurteilung war anfangs vernachlässigt worden, was zu Problemen beim Herunterfahren und Neustart führte. Wir entwickelten detaillierte Verfahren für diese Übergangsphasen, was sich als äußerst wertvoll erwies. Die Implementierung von Notfallprozeduren war eine Herausforderung, da wir das richtige Gleichgewicht zwischen Vorbereitung und Überregulierung finden mussten. Regelmäßige Übungen und Simulationen halfen uns, diese Prozeduren zu verfeinern und das Personal adäquat vorzubereiten. Ein unerwarteter Vorteil war, dass diese Übungen auch das Teamgefühl und die Kommunikation zwischen verschiedenen Abteilungen verbesserten.
Entwicklung und Implementierung eines Operations Control Programms
Einführung in das Operations Control Programm (OCP)
Als ich vor 15 Jahren bei Reinräume GmbH anfing, hatten wir kein strukturiertes Operations Control Programm (OCP) für unsere ISO 5, 7 und 8 Reinräume. Die Folge waren Inkonsistenzen in unseren Abläufen und gelegentliche Qualitätsprobleme. Die Einführung eines umfassenden OCP war eine der wichtigsten Veränderungen, die wir vorgenommen haben. Es wurde zum Rückgrat unserer Reinraumoperationen und half uns, die Kontamination effektiv zu kontrollieren. Die größte Herausforderung war es, ein Programm zu entwickeln, das sowohl umfassend als auch flexibel genug war, um auf die spezifischen Anforderungen unserer verschiedenen Reinraumklassen einzugehen.
Grundlagen unseres OCP
Unser OCP basiert auf einer gründlichen Auswirkungsbeurteilung, die wir für jeden unserer Reinräume durchgeführt haben. Dies war zunächst zeitaufwendig, erwies sich aber als unerlässlich für ein effektives Programm. Wir haben detaillierte Standardarbeitsanweisungen für alle Aspekte des Reinraumbetriebs entwickelt, von der Einrichtung über den normalen Betrieb bis hin zur Abschaltung. Eine anfängliche Schwierigkeit war es, diese Anweisungen so zu gestalten, dass sie sowohl präzise als auch benutzerfreundlich waren. Durch iterative Verbesserungen und Feedback von den Mitarbeitern konnten wir dieses Gleichgewicht schließlich finden.
Schlüsselelemente unseres OCP
Ein zentraler Bestandteil unseres OCP ist die Dokumentation des Materialflusses. Wir haben Flussdiagramme für Produkte, Rohmaterialien, Ausrüstung, Personal und Abfälle erstellt. Dies half uns, potenzielle Kontaminationsquellen zu identifizieren und zu kontrollieren. Die Implementierung eines effektiven Personalmanagementprogramms war eine weitere Herausforderung. Wir mussten nicht nur strenge Anforderungen und ein Bekleidungsprogramm entwickeln, sondern auch ein umfassendes Schulungsprogramm aufbauen. Anfangs stießen wir auf Widerstand bei einigen Mitarbeitern, aber durch kontinuierliche Kommunikation und praktische Demonstrationen konnten wir die Wichtigkeit dieser Maßnahmen vermitteln.
Reinigungs- und Wartungsprogramme
Die Entwicklung effektiver Reinigungs- und Wartungsprogramme war ein weiterer kritischer Aspekt unseres OCP. Wir lernten, dass ein „One-Size-Fits-All“-Ansatz nicht funktioniert. Stattdessen entwickelten wir maßgeschneiderte Programme für jede Reinraumklasse. Eine besondere Herausforderung war die Koordination von Reinigung und Wartung mit den Produktionsabläufen. Wir implementierten ein flexibles Schichtsystem und nutzten Produktionspausen effektiv, um diese wichtigen Aufgaben durchzuführen, ohne die Produktion zu beeinträchtigen.
Implementierung des Überwachungsprogramms
Ein robustes Überwachungsprogramm war der letzte Baustein unseres OCP. Anfangs konzentrierten wir uns hauptsächlich auf Partikelzählungen, erkannten aber bald, dass wir ein umfassenderes Monitoring benötigten. Wir integrierten Mikrobiologie-, Temperatur-, Feuchtigkeits- und Drucküberwachung in unser Programm. Die Interpretation der gesammelten Daten war zunächst eine Herausforderung. Wir investierten in Schulungen und Datenanalysesoftware, um aussagekräftige Erkenntnisse aus unseren Überwachungsdaten zu gewinnen.
Materialflussmanagement in Reinräumen: Erfahrungen und Best Practices
Einführung in das Materialflussmanagement
Als ich vor 15 Jahren bei Reinräume GmbH anfing, war unser Materialflussmanagement in den ISO 5, 7 und 8 Reinräumen eher rudimentär. Wir hatten zwar grundlegende Prozesse, aber keine systematische Herangehensweise. Dies führte oft zu Kontaminationsrisiken und Ineffizienzen. Die Implementierung eines umfassenden Materialflusssystems war eine der größten Herausforderungen, der wir uns stellen mussten. Es erforderte nicht nur technische Lösungen, sondern auch eine Änderung der Unternehmenskultur.
Entwicklung eines dokumentierten Kontrollsystems
Unser erster Schritt war die Entwicklung eines dokumentierten Systems zur Kontrolle des Materialtransfers. Anfangs war dies ein papierbasiertes System, das sich als fehleranfällig und zeitaufwendig erwies. Der Übergang zu einem digitalen System war ein Wendepunkt. Wir implementierten ein RFID-basiertes Tracking-System, das jeden Materialtransfer automatisch erfasste. Die größte Herausforderung war hier, alle Mitarbeiter im Umgang mit dem neuen System zu schulen und ihre Bedenken hinsichtlich der erhöhten Überwachung zu zerstreuen.
Evaluierung und Akzeptanz von Materialien
Ein kritischer Aspekt unseres Materialflusssystems war die Evaluierung und Akzeptanz von Materialien für den Reinraum. Wir entwickelten strenge Kriterien und Testverfahren. Anfangs führte dies zu Verzögerungen und Frustration bei einigen Lieferanten. Wir lernten, dass eine enge Zusammenarbeit mit unseren Zulieferern unerlässlich war. Wir organisierten Workshops und Schulungen für unsere Hauptlieferanten, um sie mit unseren Anforderungen vertraut zu machen. Dies führte nicht nur zu einer besseren Materialqualität, sondern auch zu innovativen Lösungen für reinraumgerechte Verpackungen.
Management von eingehenden Materialien und Komponenten
Der Umgang mit eingehenden Materialien war anfangs eine große Herausforderung. Wir implementierten ein mehrstufiges Reinigungssystem mit einer Reihe von Schleusen und Durchreichesystemen. Eine unerwartete Schwierigkeit war die Balance zwischen gründlicher Reinigung und Effizienz. Wir entwickelten spezielle Reinigungsprotokolle für verschiedene Materialtypen und investierten in fortschrittliche Reinigungstechnologien wie UV-Licht-Dekontamination. Die Schulung des Personals in diesen neuen Techniken war zeitaufwendig, zahlte sich aber durch eine signifikante Reduzierung von Kontaminationsereignissen aus.
Entsorgung von Abfällen
Die Abfallentsorgung erwies sich als komplexer als erwartet. Wir mussten nicht nur die Kontamination innerhalb des Reinraums verhindern, sondern auch lokale Umweltvorschriften einhalten. Wir implementierten ein Farbcodesystem für verschiedene Abfallarten und installierten spezielle Abfallschleusen. Eine Herausforderung war die Entsorgung von flüssigen und gasförmigen Abfällen. Wir investierten in ein geschlossenes Abfallsystem für Flüssigkeiten und ein Filtersystem für Abluft. Die Koordination mit lokalen Entsorgungsunternehmen und Behörden war zeitaufwendig, aber entscheidend für den Erfolg unseres Abfallmanagementsystems.
Transfer und Installation von großen oder stationären Geräten
Der Transfer und die Installation von großen Geräten stellte uns vor besondere Herausforderungen. Wir entwickelten detaillierte Protokolle für diese Prozesse, die eine gründliche Reinigung und Dekontamination vor dem Eintritt in den Reinraum vorsahen. In Fällen, wo eine Unterbrechung des Reinraumbetriebs unvermeidbar war, erarbeiteten wir Verfahren zur Minimierung der Ausfallzeit und zur schnellen Wiederherstellung der Reinraumbedingungen. Eine wichtige Erkenntnis war, dass eine gründliche Planung und Simulation solcher Transfers im Vorfeld viel Zeit und Ressourcen sparen kann.
Personalmanagement in Reinräumen: Erkenntnisse und Herausforderungen
Einführung in das Personalmanagement für Reinräume
Als ich vor 15 Jahren meine Arbeit bei Reinräume GmbH begann, war unser Personalmanagement für die ISO 5, 7 und 8 Reinräume eher rudimentär. Wir hatten zwar grundlegende Richtlinien, aber kein umfassendes Programm. Die Einführung eines strukturierten Personalmanagementprogramms war eine der größten Veränderungen, die wir vornahmen. Es erwies sich als entscheidend für die Aufrechterhaltung der Reinraumumgebung und die Qualität unserer Produkte.
Anforderungen und Einschränkungen für das Personal
Die Implementierung strenger Anforderungen und Einschränkungen für das Personal war anfangs eine Herausforderung. Wir mussten ein Gleichgewicht zwischen Sicherheit und Praktikabilität finden. Eine der schwierigsten Aufgaben war es, dem Personal die Notwendigkeit dieser Maßnahmen zu vermitteln. Wir entwickelten ein umfassendes Schulungsprogramm, das nicht nur die Regeln erklärte, sondern auch die wissenschaftlichen Gründe dahinter. Dies half erheblich, die Akzeptanz zu erhöhen. Eine unerwartete Herausforderung war der Umgang mit persönlichen Gegenständen. Wir mussten klare Richtlinien für Dinge wie Schmuck, Kosmetika und elektronische Geräte erstellen. Die Einführung von sicheren Aufbewahrungsmöglichkeiten außerhalb des Reinraums war eine effektive Lösung.
Implementierung eines effektiven Bekleidungsprogramms
Die Entwicklung eines effektiven Bekleidungsprogramms war ein kritischer Aspekt unseres Personalmanagements. Anfangs hatten wir Probleme mit der Passform und dem Komfort der Reinraumbekleidung, was zu Beschwerden und gelegentlichen Verstößen führte. Wir investierten in hochwertige, maßgeschneiderte Reinraumanzüge und führten ein strenges Ankleideverfahren ein. Eine besondere Herausforderung war die Schulung des Personals im korrekten An- und Ausziehen der Bekleidung. Wir installierten Spiegel und Videosysteme in den Umkleideräumen, damit die Mitarbeiter ihre Technik überprüfen konnten. Dies führte zu einer deutlichen Verbesserung der Compliance und einer Reduzierung von Kontaminationsereignissen.
Entwicklung umfassender Schulungsprogramme
Die Entwicklung umfassender Schulungsprogramme erwies sich als entscheidend für den Erfolg unseres Personalmanagements. Wir erkannten schnell, dass einmalige Schulungen nicht ausreichten. Stattdessen implementierten wir ein kontinuierliches Lernprogramm mit regelmäßigen Auffrischungskursen. Eine Herausforderung war es, die Schulungen interessant und relevant zu gestalten. Wir integrierten interaktive Elemente wie Virtual Reality-Simulationen und praktische Übungen. Ein unerwarteter Vorteil war, dass diese Schulungen auch das Teamgefühl und die Kommunikation zwischen den Mitarbeitern verbesserten.
Umgang mit Gesundheits- und Hygienefragen
Der Umgang mit Gesundheits- und Hygienefragen war ein sensibles Thema. Wir mussten strenge Richtlinien für persönliche Hygiene einführen, ohne dabei die Privatsphäre der Mitarbeiter zu verletzen. Die Einführung von Gesundheitschecks vor dem Betreten des Reinraums war anfangs umstritten. Wir lösten dies, indem wir einen Betriebsarzt einstellten und klare, faire Richtlinien für gesundheitliche Einschränkungen entwickelten. Eine besondere Herausforderung war der Umgang mit saisonalen Erkältungen und Allergien. Wir implementierten ein flexibles System, das es Mitarbeitern ermöglichte, vorübergehend andere Aufgaben außerhalb des Reinraums zu übernehmen.
Verhaltensrichtlinien und Disziplin im Reinraum
Die Entwicklung und Durchsetzung von Verhaltensrichtlinien im Reinraum war ein kontinuierlicher Prozess. Wir erkannten, dass klare Regeln allein nicht ausreichten. Stattdessen konzentrierten wir uns darauf, eine Kultur der Verantwortung und des gegenseitigen Respekts zu schaffen. Wir führten ein Buddy-System ein, bei dem erfahrene Mitarbeiter neue Kollegen betreuten. Dies half nicht nur bei der Einarbeitung, sondern förderte auch eine Kultur der gegenseitigen Unterstützung. Eine Herausforderung war der Umgang mit Verstößen gegen die Richtlinien. Wir entwickelten ein faires, aber konsequentes Disziplinarsystem, das eher auf Schulung und Verbesserung als auf Bestrafung ausgerichtet war.
Entwicklung und Umsetzung eines effektiven Reinigungsprogramms
Einführung in das Reinigungsprogramm
Als ich vor 15 Jahren bei Reinräume GmbH anfing, war unser Reinigungsprogramm für die ISO 5, 7 und 8 Reinräume zwar vorhanden, aber nicht optimal strukturiert. Wir erkannten schnell, dass ein gut durchdachtes Reinigungsprogramm entscheidend für die Aufrechterhaltung der Reinraumumgebung ist. Die Entwicklung eines umfassenden und effektiven Programms war eine der größten Herausforderungen, der wir uns stellen mussten.
Festlegung der Reinigungsanforderungen
Unser erster Schritt war die Durchführung einer gründlichen Bewertung, um die erforderlichen Reinheitsniveaus für alle Reinraumoberflächen zu bestimmen. Dies war komplexer als erwartet, da verschiedene Bereiche unterschiedliche Anforderungen hatten. Wir mussten Partikel, chemische Verunreinigungen und in einigen Bereichen auch Mikroorganismen berücksichtigen. Eine besondere Herausforderung war die Festlegung realistischer, aber strenger Grenzwerte. Wir arbeiteten eng mit unserem Qualitätssicherungsteam zusammen und führten umfangreiche Tests durch, um die optimalen Werte zu ermitteln.
Entwicklung von Reinigungsmethoden
Die Auswahl und Entwicklung geeigneter Reinigungsmethoden war ein kritischer Aspekt. Wir experimentierten mit verschiedenen Techniken, von der Trockenreinigung bis hin zu speziellen Nasswischverfahren. Eine unerwartete Herausforderung war die Kompatibilität der Reinigungsmittel mit unseren Produktionsprozessen. Wir mussten sicherstellen, dass keine Rückstände zurückblieben, die unsere Produkte beeinträchtigen könnten. Die Einführung von Reinraumstaubsaugern mit HEPA-Filtern war ein Durchbruch für die Trockenreinigung, während wir für die Nassreinigung ein System mit mehreren Eimern entwickelten, um Kreuzkontaminationen zu vermeiden.
Implementierung des Reinigungszeitplans
Die Erstellung eines effektiven Reinigungszeitplans erwies sich als Balanceakt zwischen Gründlichkeit und Produktionseffizienz. Wir mussten die Reinigungsfrequenz an die Verschmutzungsrate anpassen, die je nach Bereich und Aktivität variierte. Eine innovative Lösung war die Einführung eines dynamischen Zeitplans, der sich an die Produktionszyklen anpasste. Wir implementierten auch ein Farbcodesystem für verschiedene Reinigungsbereiche und -werkzeuge, um Verwechslungen zu vermeiden.
Schulung des Reinigungspersonals
Die Schulung unseres Reinigungspersonals war entscheidend für den Erfolg des Programms. Wir erkannten, dass Reinigung in Reinräumen eine spezialisierte Fähigkeit ist, die weit über herkömmliche Reinigungstechniken hinausgeht. Wir entwickelten ein umfassendes Schulungsprogramm, das theoretische Grundlagen und praktische Übungen umfasste. Eine Herausforderung war, das Personal für die Wichtigkeit ihrer Arbeit zu sensibilisieren. Wir führten regelmäßige Teambuilding-Aktivitäten durch und integrierten das Reinigungspersonal in Qualitätsbesprechungen, was zu einem stärkeren Engagement führte.
Überwachung und Verifikation der Reinigungseffektivität
Die Überwachung und Verifizierung der Reinigungseffektivität war ein kritischer Aspekt unseres Programms. Wir implementierten ein mehrstufiges Überwachungssystem, das visuelle Inspektionen, Oberflächenabstriche und Partikelzählungen umfasste. Eine Herausforderung war die Interpretation der Daten und die Festlegung von Aktionsgrenzen. Wir entwickelten ein computergestütztes System zur Datenanalyse, das Trends erkennen und potenzielle Probleme frühzeitig identifizieren konnte. Die Einführung von ATP-Tests für die schnelle Bewertung der mikrobiellen Belastung war ein weiterer Meilenstein in unserem Überwachungsprogramm.
Umgang mit Sonderreinigungen und Notfällen
Ein wichtiger Aspekt, den wir anfangs unterschätzten, war der Umgang mit Sonderreinigungen und Notfällen. Wir entwickelten spezielle Protokolle für unerwartete Kontaminationsereignisse, geplante Wartungsarbeiten und Anlagenmodifikationen. Eine besondere Herausforderung war die Schulung des Personals für diese Ausnahmesituationen. Wir führten regelmäßige Simulationen und Übungen durch, um die Reaktionsfähigkeit zu verbessern. Die Einrichtung eines 24/7-Bereitschaftsteams für Notfallreinigungen erwies sich als wertvoll für die Minimierung von Produktionsausfällen.
Entwicklung eines effektiven Wartungsprogramms für Reinräume
Einführung in das Wartungsprogramm
Als ich vor 15 Jahren bei Reinräume GmbH anfing, war unser Wartungsprogramm für die ISO 5, 7 und 8 Reinräume eher reaktiv als proaktiv. Wir reagierten hauptsächlich auf Probleme, anstatt sie zu verhindern. Die Entwicklung eines umfassenden, vorausschauenden Wartungsprogramms war eine der wichtigsten Veränderungen, die wir vornahmen. Es erwies sich als entscheidend für die Aufrechterhaltung der Reinraumumgebung und die Minimierung von Ausfallzeiten.
Etablierung eines dokumentierten Wartungsprogramms
Unser erster Schritt war die Erstellung eines detaillierten, dokumentierten Wartungsprogramms. Dies umfasste sowohl die Reinraumanlage selbst als auch die Produktionsausrüstung. Eine große Herausforderung war es, alle relevanten Informationen zu sammeln und zu organisieren. Wir implementierten ein computergestütztes Wartungsmanagementsystem (CMMS), das sich als unschätzbar wertvoll erwies. Es half uns, Wartungsaufgaben zu planen, zu verfolgen und zu dokumentieren. Eine unerwartete Schwierigkeit war die Integration dieses Systems mit unseren bestehenden Qualitätsmanagementprozessen. Wir mussten unsere SOPs überarbeiten und das Personal in der Nutzung des neuen Systems schulen.
Planung von Routinewartungen
Die Planung von Routinewartungen war ein Balanceakt zwischen Gründlichkeit und minimaler Störung des Produktionsablaufs. Wir führten ein System der präventiven und prädiktiven Wartung ein. Für die präventive Wartung erstellten wir detaillierte Checklisten und Zeitpläne für jedes Gerät und jede Anlage. Die prädiktive Wartung war anfangs eine Herausforderung, da sie fortschrittliche Überwachungstechnologien erforderte. Wir investierten in Sensoren und Analysesoftware, um potenzielle Probleme frühzeitig zu erkennen. Eine besondere Schwierigkeit war die Koordination der Wartungsarbeiten mit den Produktionszyklen. Wir entwickelten ein flexibles Schichtsystem für unser Wartungspersonal und nutzten Produktionspausen effektiv für Wartungsarbeiten.
Umgang mit ungeplanten Reparaturen und Modifikationen
Der Umgang mit ungeplanten Reparaturen und Modifikationen war eine der größten Herausforderungen. Wir entwickelten spezielle Verfahren, um schnell und effektiv auf unerwartete Probleme reagieren zu können, ohne die Reinraumintegrität zu gefährden. Eine innovative Lösung war die Einrichtung von „Cleanroom-in-Cleanroom“-Bereichen für Reparaturen an kritischen Geräten. Dies ermöglichte uns, Reparaturen durchzuführen, ohne den gesamten Reinraum zu kontaminieren. Wir schulten auch ein spezielles Team für Notfallreparaturen und stellten sicher, dass sie jederzeit Zugang zu den notwendigen Werkzeugen und Ersatzteilen hatten.
Spezielle Überlegungen für Wartungsarbeiten in Reinräumen
Wartungsarbeiten in Reinräumen erfordern besondere Vorkehrungen. Wir implementierten strenge Protokolle für den Eintritt von Wartungspersonal und Werkzeugen in den Reinraum. Eine Herausforderung war die Entwicklung von Wartungstechniken, die minimale Kontamination verursachen. Wir investierten in spezielle reinraumtaugliche Werkzeuge und Ausrüstungen. Bei größeren Wartungsarbeiten oder Modifikationen setzten wir temporäre Luftaufbereitungssysteme ein, um den Differenzdruck aufrechtzuerhalten. Eine unerwartete Schwierigkeit war der Umgang mit Abfällen, die bei Wartungsarbeiten entstehen. Wir entwickelten spezielle Verfahren für die sichere Entsorgung von Wartungsabfällen, einschließlich gefährlicher Materialien.
Wartung von Filtersystemen
Die Wartung unserer HEPA-Filtersysteme erwies sich als kritischer Aspekt des Programms. Wir entwickelten ein strenges Protokoll für den Austausch von Filtern, das minimale Störungen des Reinraumbetriebs gewährleistete. Eine Herausforderung war die Aufrechterhaltung der Reinraumbedingungen während des Filtertauschs. Wir implementierten ein System, bei dem wir Teile des Reinraums isolieren konnten, um Filterwechsel durchzuführen, ohne den gesamten Raum zu beeinträchtigen. Die Einführung von In-situ-Testverfahren für Filter nach ISO 14644-3 war ein wichtiger Schritt zur Verbesserung unserer Wartungseffizienz.
Schulung und Qualifikation des Wartungspersonals
Die Schulung und Qualifikation unseres Wartungspersonals war entscheidend für den Erfolg des Programms. Wir erkannten, dass Wartung in Reinräumen spezielle Kenntnisse und Fähigkeiten erfordert. Wir entwickelten ein umfassendes Schulungsprogramm, das theoretische Grundlagen der Reinraumtechnik mit praktischen Wartungstechniken verband. Eine Herausforderung war, das richtige Gleichgewicht zwischen technischem Know-how und Verständnis für Reinraumprozesse zu finden. Wir führten regelmäßige Zertifizierungen für unser Wartungspersonal ein und ermutigten sie, sich kontinuierlich weiterzubilden.
Entwicklung und Implementierung eines umfassenden Überwachungsprogramms für Reinräume
Einführung in das Überwachungsprogramm
Als ich vor 15 Jahren bei Reinräume GmbH anfing, war unser Überwachungsprogramm für die ISO 5, 7 und 8 Reinräume relativ grundlegend. Wir führten zwar regelmäßige Partikelzählungen durch, aber es fehlte ein ganzheitlicher Ansatz. Die Entwicklung eines umfassenden Überwachungsprogramms war eine der wichtigsten Verbesserungen, die wir vornahmen. Es erwies sich als entscheidend, um die Effektivität unseres Operations Control Programms (OCP) nachzuweisen und kontinuierlich zu verbessern.
Gestaltung des Überwachungsprogramms
Unser erster Schritt war die Entwicklung eines Überwachungsprogramms, das alle Aspekte unseres OCP abdeckte. Dies umfasste nicht nur die Luftreinheit, sondern auch den Materialfluss, das Personalmanagement, die Reinigung und die Wartung. Eine große Herausforderung war es, die richtigen Überwachungsparameter und -methoden für jeden Bereich zu identifizieren. Wir orientierten uns an den Normen ISO 14644-2 und ISO 14644-17 für die Luftreinheitsüberwachung und entwickelten zusätzliche Protokolle für andere Aspekte. Die Integration all dieser Elemente in ein kohärentes System war anfangs komplex, aber entscheidend für den Erfolg.
Implementierung von Umgebungsüberwachung
Die Umgebungsüberwachung war ein Kernstück unseres Programms. Wir implementierten ein kontinuierliches Partikelzählsystem in allen kritischen Bereichen, ergänzt durch regelmäßige manuelle Messungen. Eine Herausforderung war die Auswahl der richtigen Messpunkte und -intervalle. Wir führten eine detaillierte Risikoanalyse durch, um die kritischsten Bereiche zu identifizieren. Die Integration von Echtzeit-Datenerfassung und -analyse war ein Wendepunkt. Es ermöglichte uns, schnell auf Abweichungen zu reagieren und Trends frühzeitig zu erkennen.
Überwachung der Oberflächenreinheit
Die Überwachung der Oberflächenreinheit erwies sich als komplexer als erwartet. Wir implementierten ein Programm basierend auf ISO 14644-9 für Partikel und ISO 14644-10 für chemische Verunreinigungen. Eine besondere Herausforderung war die Entwicklung eines repräsentativen Stichprobenplans. Wir kombinierten regelmäßige geplante Probenahmen mit zufälligen Stichproben, um ein umfassendes Bild zu erhalten. Die Einführung von ATP-Tests für die schnelle Bewertung der mikrobiellen Belastung war ein weiterer wichtiger Schritt zur Verbesserung unserer Oberflächenüberwachung.
Personalüberwachung
Die Überwachung des Personals war ein sensibler, aber wichtiger Aspekt unseres Programms. Wir implementierten ein System zur Überprüfung der Einhaltung von Bekleidungsvorschriften und Verhaltensrichtlinien. Eine innovative Lösung war die Einführung von Videosystemen zur Analyse von Bewegungsmustern und Arbeitsabläufen. Dies half uns, potenzielle Kontaminationsquellen zu identifizieren und Schulungsprogramme zu optimieren. Eine Herausforderung war es, dies so zu gestalten, dass die Privatsphäre der Mitarbeiter respektiert wurde. Wir entwickelten strenge Datenschutzrichtlinien und involvierten den Betriebsrat in den gesamten Prozess.
Überwachung von Prozessparametern und Versorgungseinrichtungen
Die Überwachung kritischer Prozessparameter und Versorgungseinrichtungen war ein weiterer wichtiger Aspekt. Wir implementierten Systeme zur kontinuierlichen Überwachung von Temperatur, Feuchtigkeit, Druck und Luftströmung. Eine Herausforderung war die Integration dieser Daten mit unseren Produktionsprozessen. Wir entwickelten ein zentrales Überwachungssystem, das Alarme generierte, wenn Parameter außerhalb der spezifizierten Grenzen lagen. Die Implementierung von prädiktiven Analysetools half uns, potenzielle Probleme frühzeitig zu erkennen und proaktiv zu handeln.
Datenmanagement und Analyse
Das Management und die Analyse der gesammelten Daten erwies sich als eine der größten Herausforderungen. Wir implementierten ein zentrales Datenmanagementsystem, das Informationen aus verschiedenen Quellen zusammenführte. Eine besondere Schwierigkeit war die Entwicklung aussagekräftiger Berichte und Dashboards. Wir arbeiteten eng mit unserem IT-Team zusammen, um benutzerfreundliche Schnittstellen zu entwickeln, die es allen Beteiligten ermöglichten, relevante Informationen schnell zu erfassen. Die Einführung von Methoden der künstlichen Intelligenz für die Datenanalyse war ein Durchbruch, der es uns ermöglichte, komplexe Muster und Trends zu erkennen.
Kontinuierliche Verbesserung des Überwachungsprogramms
Wir erkannten schnell, dass ein statisches Überwachungsprogramm in der sich ständig weiterentwickelnden Reinraumtechnologie nicht ausreicht. Wir implementierten einen Prozess der kontinuierlichen Verbesserung, bei dem wir regelmäßig die Effektivität unseres Programms überprüften und anpassten. Eine Herausforderung war es, mit den neuesten technologischen Entwicklungen Schritt zu halten. Wir etablierten enge Beziehungen zu Forschungseinrichtungen und Technologieanbietern, um stets über Innovationen informiert zu sein.
Optimiertes Personalmanagement in Reinräumen: Erfahrungen und Best Practices

Einführung in das Personalmanagement für Reinräume
Als ich vor 15 Jahren bei Reinräume GmbH begann, unterschätzten wir die Bedeutung eines umfassenden Personalmanagements für unsere ISO 5, 7 und 8 Reinräume. Im Laufe der Zeit erkannten wir, dass der menschliche Faktor entscheidend für die Aufrechterhaltung der Reinraumumgebung ist. Die Entwicklung eines ganzheitlichen Personalmanagementansatzes wurde zu einer unserer wichtigsten Prioritäten.
Durchführung einer umfassenden Auswirkungsbeurteilung
Unser erster Schritt war die Durchführung einer gründlichen Auswirkungsbeurteilung. Wir analysierten, wie verschiedene Personalaktivitäten die Reinraumumgebung beeinflussen können. Eine besondere Herausforderung war es, alle relevanten Faktoren zu berücksichtigen – von Bewegungsmustern bis hin zu persönlichen Gewohnheiten. Wir bildeten ein interdisziplinäres Team aus Reinraumexperten, Produktionsmanagern und Personalverantwortlichen, um eine umfassende Perspektive zu gewinnen. Diese Beurteilung half uns, Prioritäten zu setzen und gezielte Maßnahmen zu entwickeln.
Entwicklung von Verantwortlichkeitsstrukturen
Ein Schlüsselelement unseres Ansatzes war die Etablierung klarer Verantwortlichkeitsstrukturen. Wir erkannten, dass Disziplin, Verhalten und persönliche Initiative entscheidend sind. Eine Herausforderung war es, diese Aspekte in unserer Unternehmenskultur zu verankern. Wir implementierten ein Mentoring-Programm, bei dem erfahrene Mitarbeiter neue Kollegen betreuten. Dies förderte nicht nur den Wissenstransfer, sondern auch ein Gefühl der gemeinsamen Verantwortung für die Reinraumumgebung.
Umgang mit persönlichen Gegenständen
Der Umgang mit persönlichen Gegenständen erwies sich als komplexer als erwartet. Wir entwickelten strenge Richtlinien für Dinge wie Schmuck, Kosmetika und elektronische Geräte. Eine besondere Herausforderung war es, diese Regeln durchzusetzen, ohne die Mitarbeiter zu demotivieren. Wir führten ein System von sicheren Aufbewahrungsmöglichkeiten außerhalb des Reinraums ein und boten alternative Lösungen an, wie z.B. reinraumtaugliche Kommunikationsgeräte. Die Einbeziehung der Mitarbeiter in die Entwicklung dieser Richtlinien erhöhte die Akzeptanz erheblich.
Implementierung strenger Hygienestandards
Die Einführung und Durchsetzung strenger Hygienestandards war ein kritischer Aspekt unseres Programms. Wir entwickelten detaillierte Protokolle für Händehygiene, Hautpflege und den Umgang mit gesundheitlichen Problemen. Eine Herausforderung war es, diese Standards konsequent einzuhalten, ohne die Produktivität zu beeinträchtigen. Wir installierten hochmoderne Händehygienestationen und führten regelmäßige Schulungen durch. Die Einführung von UV-Kontrollsystemen zur Überprüfung der Händehygiene war anfangs umstritten, erwies sich aber als effektives Instrument zur Sensibilisierung.
Kontrolle des Personalzugangs
Die Kontrolle des Personalzugangs zu unseren Reinräumen war ein weiterer kritischer Aspekt. Wir implementierten ein mehrstufiges Zugangssystem mit biometrischer Authentifizierung. Eine Herausforderung war es, den Zugang für essentielles Personal zu gewährleisten, während unnötige Eintritte minimiert wurden. Wir entwickelten ein dynamisches Zugangsmanagement-System, das sich an die aktuellen Produktionsanforderungen anpasste. Die Integration von Besuchermanagement in dieses System war komplex, aber entscheidend für die Aufrechterhaltung unserer Reinraumintegrität.
Schulung und kontinuierliche Weiterbildung
Wir erkannten schnell, dass regelmäßige Schulungen und Weiterbildungen essenziell sind. Wir entwickelten ein umfassendes Trainingsprogramm, das theoretische Grundlagen mit praktischen Übungen verband. Eine besondere Herausforderung war es, die Schulungen interessant und relevant zu gestalten. Wir integrierten interaktive Elemente wie Virtual Reality-Simulationen und Gamification-Ansätze. Die Einführung eines Online-Lernmanagementsystems ermöglichte es uns, den Fortschritt jedes Mitarbeiters zu verfolgen und individualisierte Lernpfade anzubieten.
Umgang mit psychologischen Faktoren
Ein oft übersehener Aspekt des Personalmanagements in Reinräumen sind die psychologischen Faktoren. Wir stellten fest, dass die Arbeit in einer kontrollierten Umgebung für manche Mitarbeiter belastend sein kann. Wir implementierten ein Unterstützungsprogramm, das psychologische Beratung und Stressmanagement-Techniken anbot. Die Einrichtung von „Erholungszonen“ außerhalb der Reinräume, wo Mitarbeiter kurze Pausen einlegen konnten, erwies sich als besonders wertvoll für das Wohlbefinden und die Produktivität.
Optimierung des Bekleidungsprogramms in Reinräumen: Erfahrungen und Innovationen
Einführung in das Bekleidungsprogramm
Als ich vor 15 Jahren bei Reinräume GmbH anfing, war unser Bekleidungsprogramm für die ISO 5, 7 und 8 Reinräume zwar funktional, aber nicht optimal. Im Laufe der Zeit erkannten wir, dass ein durchdachtes Bekleidungsprogramm entscheidend für die Aufrechterhaltung der Reinraumumgebung ist. Die Entwicklung eines effizienten und benutzerfreundlichen Bekleidungsprozesses wurde zu einer unserer Top-Prioritäten.
Berücksichtigung der Auswirkungsbeurteilung
Unser erster Schritt war die Integration der Ergebnisse unserer Auswirkungsbeurteilung in das Bekleidungsprogramm. Wir analysierten genau, wie verschiedene Bekleidungsaspekte die Reinraumumgebung beeinflussen. Eine besondere Herausforderung war es, die richtige Balance zwischen Schutz und Komfort zu finden. Wir führten umfangreiche Tests durch, um die Partikelfreisetzung verschiedener Materialien und Bekleidungsdesigns zu bewerten. Diese Daten halfen uns, fundierte Entscheidungen über die Auswahl unserer Reinraumbekleidung zu treffen.
Auswahl geeigneter Materialien und Designs
Die Auswahl der richtigen Materialien und Designs für unsere Reinraumbekleidung war ein kritischer Aspekt. Wir suchten nach Stoffen, die eine optimale Barrierewirkung, Festigkeit und geringe Flusenbildung aufwiesen. Eine Herausforderung war es, Materialien zu finden, die diese Eigenschaften mit ausreichendem Tragekomfort verbinden. Wir arbeiteten eng mit Herstellern zusammen, um maßgeschneiderte Lösungen zu entwickeln. Die Einführung von atmungsaktiven, aber hocheffektiven Materialien war ein Durchbruch, der sowohl die Kontaminationskontrolle als auch den Mitarbeiterkomfort verbesserte.
Entwicklung eines effizienten Ankleideverfahrens
Die Entwicklung eines effizienten und sicheren Ankleideverfahrens war entscheidend. Wir implementierten ein schrittweises Ankleideverfahren, das Kreuzkontaminationen minimiert. Eine besondere Herausforderung war es, dieses Verfahren so zu gestalten, dass es für alle Mitarbeiter leicht zu befolgen war. Wir installierten visuelle Anleitungen und Spiegel in den Umkleideräumen und führten ein Buddy-System ein, bei dem sich die Mitarbeiter gegenseitig beim korrekten Ankleiden unterstützen. Die Einführung von RFID-Technologie zur Verfolgung der Bekleidungsnutzung half uns, die Einhaltung der Vorschriften zu überwachen und den Bekleidungswechsel zu optimieren.
Umgang mit Mehrfachverwendung und Lebensdauer
Der Umgang mit der Mehrfachverwendung von Bekleidung und die Bestimmung der optimalen Lebensdauer waren komplexe Themen. Wir entwickelten ein System zur Überwachung der Bekleidungsqualität über mehrere Verwendungen hinweg. Eine Herausforderung war es, den richtigen Zeitpunkt für den Austausch zu bestimmen. Wir implementierten ein Punktesystem, das verschiedene Faktoren wie Verwendungshäufigkeit, Waschzyklen und visuelle Inspektionen berücksichtigte. Die Einführung von speziellen Reinigungsverfahren, die die Lebensdauer der Bekleidung verlängerten, ohne ihre Schutzfunktion zu beeinträchtigen, war ein wichtiger Durchbruch.
Lagerung und Handhabung der Bekleidung
Die korrekte Lagerung und Handhabung der Reinraumbekleidung erwies sich als kritischer Faktor. Wir entwickelten ein System zur kontrollierten Aufbewahrung, das Kontaminationen während der Lagerung verhindert. Eine Herausforderung war die Gestaltung eines effizienten Logistiksystems für die Bekleidung. Wir implementierten ein automatisiertes Lagersystem mit Ausgabeautomaten, das die Verfügbarkeit sauberer Bekleidung optimierte und gleichzeitig den menschlichen Kontakt minimierte. Die Integration dieses Systems in unseren Workflow verbesserte nicht nur die Hygiene, sondern auch die Effizienz des gesamten Ankleideprozesses.
Schulung und Compliance
Ein entscheidender Aspekt unseres Bekleidungsprogramms war die gründliche Schulung aller Mitarbeiter. Wir entwickelten ein umfassendes Trainingsprogramm, das theoretische Grundlagen mit praktischen Übungen verband. Eine besondere Herausforderung war es, die Wichtigkeit der korrekten Bekleidung kontinuierlich zu vermitteln. Wir führten regelmäßige Auffrischungskurse und Compliance-Checks ein. Die Einführung von gamifizierten Schulungselementen und Wettbewerben für die beste Ankleidetechnik erhöhte das Engagement und die Einhaltung der Vorschriften erheblich.
Entwicklung eines effektiven Schulungsprogramms für Reinräume: Erfahrungen und Innovationen
Einführung in das Schulungsprogramm
Als ich vor 15 Jahren bei Reinräume GmbH anfing, war unser Schulungsprogramm für die ISO 5, 7 und 8 Reinräume eher rudimentär. Im Laufe der Zeit erkannten wir, dass ein umfassendes und effektives Schulungsprogramm der Schlüssel zur Aufrechterhaltung höchster Reinraumstandards ist. Die Entwicklung eines innovativen und nachhaltigen Schulungskonzepts wurde zu einer unserer Hauptprioritäten.
Gestaltung eines maßgeschneiderten Schulungsprogramms
Unser erster Schritt war die Entwicklung eines maßgeschneiderten Schulungsprogramms, das auf die spezifischen Anforderungen unserer verschiedenen Mitarbeitergruppen zugeschnitten war. Wir erkannten, dass Manager, Produktionstechniker, Qualitätsmitarbeiter, Forscher, Ingenieure, Wartungs- und Servicetechniker sowie Vertragsmitarbeiter und Besucher unterschiedliche Schulungsbedürfnisse haben. Eine besondere Herausforderung war es, relevante und praxisnahe Schulungsinhalte für jede Gruppe zu entwickeln. Wir bildeten ein interdisziplinäres Team aus Reinraumexperten, Pädagogen und Fachspezialisten, um ganzheitliche Schulungsmodule zu erstellen.
Implementierung kontinuierlicher Lernprozesse
Die Einführung eines Systems für kontinuierliches Lernen war entscheidend. Wir erkannten schnell, dass einmalige Schulungen nicht ausreichten, um die Fähigkeiten und das Wissen unserer Mitarbeiter auf dem neuesten Stand zu halten. Wir implementierten ein Programm mit regelmäßigen Auffrischungskursen und Weiterbildungsmöglichkeiten. Eine Herausforderung war es, diese Schulungen in den Arbeitsalltag zu integrieren, ohne die Produktivität zu beeinträchtigen. Die Einführung von flexiblen Online-Lernmodulen und Mikro-Lerneinheiten, die in kurzen Pausen absolviert werden konnten, erwies sich als effektive Lösung.
Entwicklung interaktiver Schulungsmethoden
Um die Effektivität unserer Schulungen zu erhöhen, setzten wir auf interaktive und praxisorientierte Methoden. Wir integrierten Simulationen, Rollenspiele und praktische Übungen in unser Programm. Eine besondere Innovation war die Einführung von Virtual Reality (VR) Trainings, die es den Mitarbeitern ermöglichten, kritische Reinraumprozesse in einer risikofreien Umgebung zu üben. Die Entwicklung dieser VR-Szenarien war anfangs kostspielig, zahlte sich aber durch verbesserte Lerneffekte und reduzierte Fehler in der realen Umgebung aus.
Qualifikation und Zertifizierung
Die Einführung eines robusten Qualifikations- und Zertifizierungssystems war ein weiterer Schwerpunkt unseres Programms. Wir entwickelten klare Kriterien für die initiale Qualifikation und regelmäßige Requalifizierung der Mitarbeiter. Eine Herausforderung war es, ein System zu schaffen, das sowohl rigoros als auch fair war. Wir implementierten ein mehrstufiges Bewertungssystem, das theoretisches Wissen, praktische Fähigkeiten und Verhaltensaspekte berücksichtigte. Die Einführung digitaler Badges und Zertifikate erhöhte die Motivation der Mitarbeiter und schuf eine Kultur des kontinuierlichen Lernens.
Dokumentation und Nachverfolgung
Ein effektives System zur Dokumentation und Nachverfolgung der Schulungen war entscheidend für den Erfolg unseres Programms. Wir implementierten ein digitales Lernmanagementsystem (LMS), das es uns ermöglichte, Schulungsaktivitäten, -ergebnisse und Zertifizierungen zu verfolgen. Eine Herausforderung war die Integration dieses Systems mit unseren bestehenden HR- und Qualitätsmanagement-Systemen. Die Entwicklung von individuellen Lernpfaden und automatisierten Erinnerungen für fällige Schulungen verbesserte die Compliance und erleichterte die Planung.
Schulung für Notfallsituationen
Ein oft vernachlässigter Aspekt, dem wir besondere Aufmerksamkeit widmeten, war die Schulung für Notfallsituationen in Reinräumen. Wir entwickelten spezielle Module für den Umgang mit Kontaminationsereignissen, technischen Ausfällen und medizinischen Notfällen. Eine innovative Lösung war die Durchführung regelmäßiger Notfallsimulationen unter realistischen Bedingungen. Diese Übungen halfen nicht nur, die Reaktionsfähigkeit zu verbessern, sondern deckten auch Schwachstellen in unseren Prozessen auf.
Entwicklung eines effektiven Reinigungsprogramms für Reinräume: Erfahrungen und Best Practices

Einführung in das Reinigungsprogramm
Als ich vor 15 Jahren bei Reinräume GmbH anfing, war unser Reinigungsansatz für die ISO 5, 7 und 8 Reinräume zwar grundlegend funktional, aber nicht optimal strukturiert. Im Laufe der Zeit erkannten wir, dass ein durchdachtes und systematisches Reinigungsprogramm entscheidend für die Aufrechterhaltung der Reinraumumgebung ist. Die Entwicklung eines umfassenden und effektiven Reinigungsprogramms wurde zu einer unserer Hauptprioritäten.
Identifizierung und Klassifizierung von Reinraumoberflächen
Unser erster Schritt war die genaue Identifizierung und Klassifizierung aller Reinraumoberflächen. Wir unterteilten unsere Reinräume in verschiedene Zonen und kategorisierten die Oberflächen nach ihrer Kritikalität. Eine besondere Herausforderung war die Bestimmung der erforderlichen Reinheitsgrade für jede Oberfläche. Wir führten umfangreiche Tests durch, um die Kontaminationsrisiken und -quellen für jede Oberfläche zu bewerten. Diese detaillierte Analyse half uns, maßgeschneiderte Reinigungsprotokolle für jede Oberflächenart zu entwickeln.
Entwicklung geeigneter Reinigungsmethoden
Die Auswahl und Entwicklung geeigneter Reinigungsmethoden war ein kritischer Aspekt unseres Programms. Wir experimentierten mit verschiedenen Techniken, von der Trockenreinigung bis hin zu speziellen Nasswischverfahren. Eine besondere Herausforderung war die Auswahl von Reinigungsmitteln, die effektiv, aber gleichzeitig schonend für die Oberflächen und kompatibel mit unseren Produktionsprozessen waren. Wir arbeiteten eng mit Chemieexperten zusammen, um maßgeschneiderte Reinigungslösungen zu entwickeln. Die Einführung von elektrostatisch geladenen Mikrofasertüchern für die Trockenreinigung und die Verwendung von Reinigungsrobotern in bestimmten Bereichen waren innovative Lösungen, die unsere Reinigungseffizienz deutlich verbesserten.
Erstellung detaillierter Reinigungsanweisungen
Die Entwicklung detaillierter und leicht verständlicher Reinigungsanweisungen war entscheidend für den Erfolg unseres Programms. Wir erstellten Schritt-für-Schritt-Anleitungen für jede Reinigungsaufgabe, einschließlich Informationen zu den zu verwendenden Materialien, Techniken und Sicherheitsmaßnahmen. Eine Herausforderung war es, diese Anweisungen so zu gestalten, dass sie für alle Mitarbeiter, unabhängig von ihrem Hintergrund, leicht zu verstehen und zu befolgen waren. Die Verwendung von visuellen Hilfsmitteln wie Infografiken und Kurzvideos erwies sich als besonders effektiv.
Implementierung von Reinigungszeitplänen
Die Erstellung und Umsetzung effektiver Reinigungszeitpläne war ein weiterer kritischer Aspekt. Wir mussten die Häufigkeit der Reinigung für jede Oberfläche und Zone festlegen, basierend auf Faktoren wie Kontaminationsrisiko und Nutzungsintensität. Eine besondere Herausforderung war die Integration der Reinigungsaktivitäten in den Produktionsablauf, ohne die Effizienz zu beeinträchtigen. Wir entwickelten ein dynamisches Zeitplanungssystem, das sich an die Produktionszyklen anpasste und Reinigungsaktivitäten in Produktionspausen optimierte.
Überwachung der Reinigungseffektivität
Die Überwachung und Verifizierung der Reinigungseffektivität war ein entscheidender Bestandteil unseres Programms. Wir implementierten ein mehrstufiges Überwachungssystem, das visuelle Inspektionen, Oberflächenabstriche und fortschrittliche Messtechniken umfasste. Eine Herausforderung war die Festlegung realistischer, aber strenger Grenzwerte für die Oberflächenreinheit. Wir entwickelten ein datenbasiertes System zur kontinuierlichen Verbesserung, das es uns ermöglichte, Trends zu erkennen und unsere Reinigungsprotokolle entsprechend anzupassen.
Schulung und Qualifikation des Reinigungspersonals
Die gründliche Schulung und Qualifikation unseres Reinigungspersonals war entscheidend für den Erfolg des Programms. Wir entwickelten ein umfassendes Schulungsprogramm, das theoretisches Wissen mit praktischen Übungen verband. Eine besondere Herausforderung war es, das Bewusstsein für die kritische Bedeutung der Reinigung in Reinräumen zu schärfen. Wir führten regelmäßige Zertifizierungen und Leistungsbewertungen ein, um die Qualität der Reinigungsarbeit sicherzustellen. Die Einführung eines Karrierepfads für Reinigungsspezialisten erhöhte die Motivation und Professionalität unseres Teams erheblich.
Umgang mit Sonderreinigungen und Notfällen
Ein wichtiger Aspekt, den wir anfangs unterschätzten, war der Umgang mit Sonderreinigungen und Notfällen. Wir entwickelten spezielle Protokolle für unerwartete Kontaminationsereignisse, geplante Wartungsarbeiten und Anlagenmodifikationen. Eine besondere Herausforderung war die Schulung des Personals für diese Ausnahmesituationen. Wir führten regelmäßige Simulationen und Übungen durch, um die Reaktionsfähigkeit zu verbessern.
15 Jahre Reinraum-Management bei Reinräume GmbH: Schlüsselerfahrungen und Zukunftsausblick

Einführung
Nach 15 Jahren intensiver Arbeit im Reinraum-Management bei Reinräume GmbH möchte ich die wichtigsten Erkenntnisse und Erfahrungen teilen, die wir bei der Optimierung unserer ISO 5, 7 und 8 Reinräume gesammelt haben. Dieser Rückblick soll andere Reinraumbetreiber inspirieren und einen Ausblick auf zukünftige Entwicklungen in der Reinraumtechnologie geben.
Ganzheitlicher Ansatz als Schlüssel zum Erfolg
Eine unserer wichtigsten Erkenntnisse war die Notwendigkeit eines ganzheitlichen Ansatzes im Reinraum-Management. Wir lernten, dass alle Aspekte – von der Auswirkungsbeurteilung über das Personalmanagement bis hin zur Reinigung – eng miteinander verwoben sind. Die Implementierung eines umfassenden Operations Control Programms (OCP) erwies sich als entscheidend für die Koordination aller Aktivitäten und die Aufrechterhaltung höchster Qualitätsstandards.
Bedeutung des menschlichen Faktors
Eine überraschende Erkenntnis war die immense Bedeutung des menschlichen Faktors in Reinräumen. Wir investierten stark in Personalmanagement, Schulung und die Entwicklung einer Reinraumkultur. Die Einführung interaktiver Schulungsmethoden, einschließlich Virtual Reality-Simulationen, verbesserte nicht nur die Fähigkeiten unserer Mitarbeiter, sondern auch ihr Verständnis für die Kritikalität ihrer Arbeit.
Technologische Innovationen als Treiber der Verbesserung
Der Einsatz neuer Technologien war ein Schlüsselfaktor für unsere kontinuierliche Verbesserung. Von RFID-Systemen für das Bekleidungsmanagement bis hin zu KI-gestützten Überwachungssystemen – technologische Innovationen halfen uns, Prozesse zu optimieren und die Reinraumleistung zu steigern. Besonders die Integration von IoT-Geräten zur Echtzeitüberwachung von Umgebungsparametern revolutionierte unser Verständnis der Reinraumdynamik.
Flexibilität und Anpassungsfähigkeit
Die Fähigkeit, flexibel auf neue Herausforderungen zu reagieren, erwies sich als entscheidend. Wir entwickelten adaptive Systeme für Reinigung, Wartung und Schulung, die sich an verändernde Produktionsanforderungen anpassen konnten. Die COVID-19-Pandemie unterstrich die Bedeutung dieser Flexibilität und führte zur Einführung neuer Hygiene- und Sicherheitsprotokolle.
Datengesteuerte Entscheidungsfindung
Die Implementierung umfassender Datenerfassungs- und Analysesysteme verbesserte unsere Entscheidungsprozesse erheblich. Wir konnten Trends frühzeitig erkennen, proaktiv auf potenzielle Probleme reagieren und unsere Ressourcen effizienter einsetzen. Die Entwicklung von prädiktiven Modellen für die Reinraumleistung war ein besonderer Durchbruch.
Nachhaltigkeit als neue Herausforderung
In den letzten Jahren rückte das Thema Nachhaltigkeit zunehmend in den Fokus. Wir begannen, energieeffizientere Systeme zu implementieren, den Wasserverbrauch zu optimieren und umweltfreundlichere Reinigungsmethoden zu entwickeln. Die Balance zwischen strenger Kontaminationskontrolle und Umweltverträglichkeit bleibt eine spannende Herausforderung für die Zukunft.
Zukunftsausblick
Blickend in die Zukunft, sehe ich mehrere Trends, die die Reinraumtechnologie weiter prägen werden:
- Verstärkter Einsatz von Automatisierung und Robotik, insbesondere in hochkritischen Bereichen.
- Weiterentwicklung von KI-gestützten Überwachungs- und Steuerungssystemen für eine noch präzisere Kontrolle der Reinraumumgebung.
- Fortschritte in der Materialwissenschaft, die zu effektiveren und nachhaltigeren Reinraumbekleidungen und -oberflächen führen.
- Verstärkte Integration von Augmented Reality in Schulungs- und Betriebsabläufe.
- Entwicklung von „intelligenten Reinräumen“, die sich selbst überwachen und anpassen können.
12 Replies to “Reinräume ISO 8, ISO 7, ISO 5 – aus der Sicht eines Praktikers”
Die Implementierung eines umfassenden Personalmanagementprogramms bei Reinräume GmbH war ein fortlaufender Prozess mit vielen Lernmomenten. Wir erkannten, dass der menschliche Faktor in Reinräumen oft unterschätzt wird, aber entscheidend für den Erfolg ist. Für andere Reinraumbetreiber empfehle ich, von Anfang an in ein robustes Personalmanagementprogramm zu investieren. Wichtig ist dabei, die Mitarbeiter als Partner im Prozess zu sehen und ihre Ideen und Bedenken ernst zu nehmen. Kontinuierliche Schulung, klare Kommunikation und die Schaffung einer positiven Reinraumkultur sind Schlüsselfaktoren für den Erfolg. Unser Personalmanagementprogramm hat nicht nur die Qualität und Effizienz unserer Reinräume verbessert, sondern auch zu einer höheren Arbeitszufriedenheit und geringeren Fluktuation geführt. Es ist heute ein zentraler Bestandteil unseres Erfolgs bei Reinräume GmbH.
Die Entwicklung und Implementierung eines umfassenden Überwachungsprogramms bei Reinräume GmbH war ein kontinuierlicher Lernprozess. Wir erkannten, dass effektive Überwachung weit mehr ist als nur Datensammlung – es ist ein strategisches Tool für Qualitätssicherung und Prozessoptimierung. Für andere Reinraumbetreiber empfehle ich, von Anfang an in ein gut durchdachtes, integriertes Überwachungsprogramm zu investieren.
Eine wichtige Erkenntnis war, dass ein effektives Überwachungsprogramm nicht nur zur Einhaltung von Vorschriften beiträgt, sondern auch erhebliche betriebliche Vorteile bietet. Es ermöglicht eine proaktive Problemlösung, optimiert Ressourceneinsatz und unterstützt datengetriebene Entscheidungsprozesse.
Heute ist unser Überwachungsprogramm ein Vorzeigeprojekt bei Reinräume GmbH und hat wesentlich zu unserem Ruf als innovativer und zuverlässiger Reinraumbetreiber beigetragen. Es unterstreicht, dass ein gut konzipiertes Überwachungsprogramm ein mächtiges Werkzeug für die kontinuierliche Verbesserung und Wettbewerbsfähigkeit in der Reinraumtechnologie ist.
Rückblickend war der Weg zu unserem heutigen Ansatz der Auswirkungsbeurteilung von vielen Lernprozessen geprägt. Wir erkannten, dass Flexibilität und kontinuierliche Verbesserung entscheidend sind. Ein wichtiger Lerneffekt war, dass die Einbeziehung aller Mitarbeiterebenen zu besseren und praxisnäheren Lösungen führt. Für Neueinsteiger im Reinraummanagement rate ich, von Anfang an einen ganzheitlichen Ansatz zu verfolgen und offen für Feedback zu sein. Die Investition in gründliche Schulungen und die Schaffung einer Kultur der kontinuierlichen Verbesserung zahlen sich langfristig aus. Eine unerwartete Erkenntnis war, wie wichtig es ist, technische Aspekte mit menschlichen Faktoren in Einklang zu bringen. Unsere Erfahrung bei Reinräume GmbH zeigt deutlich, dass eine gut durchgeführte Auswirkungsbeurteilung der Schlüssel zu einem erfolgreichen und effizienten Reinraumbetrieb ist, aber auch, dass sie ein lebendiger Prozess ist, der ständiger Anpassung und Verfeinerung bedarf.
Die Entwicklung und Umsetzung eines effektiven Reinigungsprogramms bei Reinräume GmbH war ein kontinuierlicher Lernprozess. Wir erkannten, dass Reinigung in Reinräumen weit mehr ist als nur das Entfernen von Schmutz – es ist ein kritischer Aspekt der Qualitätskontrolle und Produktsicherheit. Für andere Reinraumbetreiber empfehle ich, von Anfang an in ein gut durchdachtes Reinigungsprogramm zu investieren. Wichtig ist dabei, das Programm als integralen Bestandteil des gesamten Reinraumbetriebs zu betrachten und nicht als isolierte Aktivität.
Eine unerwartete Erkenntnis war, wie sehr ein effektives Reinigungsprogramm zur allgemeinen Betriebseffizienz beitragen kann. Durch die Optimierung unserer Reinigungsprozesse konnten wir nicht nur die Reinraumqualität verbessern, sondern auch Produktionsunterbrechungen reduzieren und die Gesamtproduktivität steigern.
Heute ist unser Reinigungsprogramm ein Vorzeigeprojekt bei Reinräume GmbH und hat wesentlich zu unserem Ruf als führender Reinraumbetreiber beigetragen. Es unterstreicht, dass selbst scheinbar grundlegende Aspekte wie Reinigung, wenn sie professionell und wissenschaftlich angegangen werden, einen bedeutenden Einfluss auf den Gesamterfolg eines Reinraumbetriebs haben können.
Die Entwicklung und Optimierung unseres Bekleidungsprogramms bei Reinräume GmbH war ein kontinuierlicher Lernprozess. Wir erkannten, dass ein effektives Bekleidungsprogramm weit mehr ist als nur das Bereitstellen von Schutzkleidung – es ist ein integraler Bestandteil der Kontaminationskontrolle und der Reinraumkultur. Für andere Reinraumbetreiber empfehle ich, von Anfang an in ein durchdachtes, benutzerfreundliches Bekleidungsprogramm zu investieren.
Eine wichtige Erkenntnis war, dass die Einbeziehung der Mitarbeiter in die Entwicklung und Verbesserung des Bekleidungsprogramms zu besserer Akzeptanz und Compliance führt. Die kontinuierliche Investition in neue Technologien und Materialien zahlt sich langfristig durch verbesserte Reinraumleistung und Mitarbeiterzufriedenheit aus.
Heute ist unser Bekleidungsprogramm ein Vorzeigeprojekt bei Reinräume GmbH und hat wesentlich zu unserem Ruf als innovativer und qualitätsorientierter Reinraumbetreiber beigetragen. Es unterstreicht, dass ein gut konzipiertes Bekleidungsprogramm nicht nur eine Notwendigkeit, sondern ein strategischer Vorteil in der Reinraumtechnologie ist.
Die Entwicklung und Umsetzung eines effektiven Wartungsprogramms bei Reinräume GmbH war ein kontinuierlicher Lernprozess. Wir erkannten, dass Wartung in Reinräumen weit mehr ist als nur die Reparatur von Geräten – es ist ein integraler Bestandteil der Qualitätssicherung und Kontaminationskontrolle. Für andere Reinraumbetreiber empfehle ich, von Anfang an in ein durchdachtes, proaktives Wartungsprogramm zu investieren.
Eine wichtige Erkenntnis war, dass ein effektives Wartungsprogramm nicht nur Ausfallzeiten reduziert, sondern auch die Gesamtlebensdauer der Anlagen verlängert und die Betriebskosten senkt. Die Integration von Wartung in den gesamten Reinraumbetrieb, einschließlich Schulung, Dokumentation und Qualitätskontrolle, war entscheidend für unseren Erfolg.
Heute ist unser Wartungsprogramm ein Vorzeigeprojekt bei Reinräume GmbH und hat wesentlich zu unserem Ruf als zuverlässiger und effizienter Reinraumbetreiber beigetragen. Es unterstreicht, dass ein gut durchdachtes Wartungsprogramm nicht nur ein notwendiger Kostenfaktor ist, sondern einen erheblichen Mehrwert für den gesamten Reinraumbetrieb schafft.
Die letzten 15 Jahre bei Reinräume GmbH haben gezeigt, dass erfolgreiches Reinraum-Management eine Kombination aus technischem Know-how, innovativem Denken und einem tiefen Verständnis für menschliche Faktoren erfordert. Die kontinuierliche Verbesserung und Anpassung an neue Herausforderungen bleiben der Schlüssel zum Erfolg in dieser dynamischen Branche.
Für die Zukunft bin ich überzeugt, dass Reinräume eine noch kritischere Rolle in vielen Industriezweigen spielen werden. Die Fähigkeit, hochreine Umgebungen effizient und nachhaltig zu betreiben, wird zu einem entscheidenden Wettbewerbsvorteil. Bei Reinräume GmbH sind wir stolz darauf, an der Spitze dieser Entwicklung zu stehen, und freuen uns darauf, die Reinraumtechnologie auch in den kommenden Jahren weiterzuentwickeln und zu verbessern.
Die Entwicklung eines umfassenden Personalmanagementprogramms für unsere Reinräume bei Reinräume GmbH war ein kontinuierlicher Lernprozess. Wir erkannten, dass der menschliche Faktor der Schlüssel zu einem erfolgreichen Reinraumbetrieb ist. Für andere Reinraumbetreiber empfehle ich, von Anfang an in ein ganzheitliches Personalmanagement zu investieren, das technische Anforderungen mit menschlichen Bedürfnissen in Einklang bringt.
Eine wichtige Erkenntnis war, dass ein effektives Personalmanagement nicht nur die Reinraumleistung verbessert, sondern auch zu höherer Mitarbeiterzufriedenheit und geringerer Fluktuation führt. Die Schaffung einer Kultur, in der jeder Mitarbeiter die Bedeutung seiner Rolle für die Reinraumintegrität versteht und wertschätzt, war entscheidend für unseren Erfolg.
Heute ist unser Personalmanagementprogramm ein Vorzeigeprojekt bei Reinräume GmbH und hat wesentlich zu unserem Ruf als innovativer und mitarbeiterorientierter Reinraumbetreiber beigetragen. Es unterstreicht, dass ein gut konzipiertes Personalmanagement nicht nur eine Notwendigkeit, sondern ein strategischer Vorteil in der Reinraumtechnologie ist.
Die Entwicklung und kontinuierliche Verbesserung unseres Schulungsprogramms bei Reinräume GmbH war ein dynamischer Prozess. Wir erkannten, dass effektives Training der Schlüssel zur Aufrechterhaltung höchster Qualitätsstandards und zur Förderung einer Kultur der kontinuierlichen Verbesserung ist. Für andere Reinraumbetreiber empfehle ich, von Anfang an in ein umfassendes, innovatives Schulungsprogramm zu investieren.
Eine wichtige Erkenntnis war, dass Schulung nicht als einmaliger Event, sondern als kontinuierlicher Prozess betrachtet werden sollte. Die Integration von Technologie, die Personalisierung von Lernpfaden und die Schaffung einer Lernkultur waren entscheidend für unseren Erfolg.
Heute ist unser Schulungsprogramm ein Vorzeigeprojekt bei Reinräume GmbH und hat wesentlich zu unserem Ruf als Exzellenzzentrum in der Reinraumtechnologie beigetragen. Es unterstreicht, dass gut geschultes Personal nicht nur ein Kostenfaktor, sondern ein entscheidender Wettbewerbsvorteil in der anspruchsvollen Welt der Reinraumtechnologie ist.
Die Entwicklung und kontinuierliche Verbesserung unseres Reinigungsprogramms bei Reinräume GmbH war ein dynamischer Prozess voller Lernmöglichkeiten. Wir erkannten, dass effektive Reinigung in Reinräumen weit mehr ist als nur das Entfernen von Schmutz – es ist ein kritischer Aspekt der Qualitätskontrolle und Produktsicherheit. Für andere Reinraumbetreiber empfehle ich, von Anfang an in ein gut durchdachtes, wissenschaftlich fundiertes Reinigungsprogramm zu investieren.
Eine wichtige Erkenntnis war, dass ein erfolgreiches Reinigungsprogramm Flexibilität und kontinuierliche Anpassung erfordert. Die Integration neuer Technologien, die ständige Schulung des Personals und die datengestützte Optimierung der Prozesse waren Schlüsselfaktoren für unseren Erfolg.
Heute ist unser Reinigungsprogramm ein Vorzeigeprojekt bei Reinräume GmbH und hat wesentlich zu unserem Ruf als führender Reinraumbetreiber beigetragen. Es unterstreicht, dass ein gut konzipiertes und umgesetztes Reinigungsprogramm nicht nur eine Notwendigkeit, sondern ein strategischer Vorteil in der anspruchsvollen Welt der Reinraumtechnologie ist.
Die Implementierung eines effektiven Materialflusssystems in unseren Reinräumen bei Reinräume GmbH war ein kontinuierlicher Lernprozess. Wir erkannten, dass Flexibilität und die Bereitschaft zur ständigen Verbesserung entscheidend sind. Für andere Reinraumbetreiber empfehle ich, von Anfang an ein ganzheitliches Materialflusssystem zu implementieren und dabei alle Stakeholder einzubeziehen. Investitionen in Technologie und Schulungen zahlen sich langfristig aus. Eine unerwartete Erkenntnis war, wie sehr ein gut durchdachtes Materialflusssystem nicht nur die Kontaminationskontrolle verbessert, sondern auch die Gesamteffizienz des Reinraumbetriebs steigert. Heute ist unser Materialflussmanagement ein Vorzeigeprojekt bei Reinräume GmbH und hat wesentlich zu unserem Ruf als führender Reinraumbetreiber beigetragen.
Die Implementierung unseres OCP war ein fortlaufender Prozess mit vielen Lernmomenten. Wir erkannten, dass ein erfolgreiches OCP nicht statisch sein kann, sondern sich ständig weiterentwickeln muss. Regelmäßige Überprüfungen und Anpassungen wurden zu einem festen Bestandteil unseres Programms. Eine wichtige Erkenntnis war, dass die Einbindung aller Mitarbeiter, von den Reinigungskräften bis zum Management, entscheidend für den Erfolg ist. Für andere Reinraumbetreiber empfehle ich, von Anfang an ein umfassendes OCP zu entwickeln, aber flexibel genug zu bleiben, um aus Erfahrungen zu lernen und sich anzupassen. Bei Reinräume GmbH hat unser OCP nicht nur die Qualität und Effizienz unserer Reinräume verbessert, sondern auch zu einer Kultur der kontinuierlichen Verbesserung beigetragen, die weit über den Reinraumbetrieb hinausgeht.